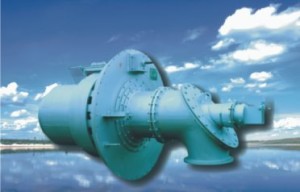
Swirl burners are designed for coal dust combustion in power boilers with burner wall socket system. The design of the burner allows the distribution of dust-air mixture into two streams with different concentrations of dust.
The density of dust is in the axis of the burner, which helps to reduce the intensity of the production of nitrogen oxides. The advantage is NOx reduction rate exceeding 50%, high flame stability and long lifetime achieved by the use of heat-resistant and abrasion-resistant materials.
Jet burners are designed for combustion of coal dust in boilers with tangential furnace. Its design allows the combustion air stream to be introduced tangentialy into the vortex circle parallel to the stream of coal dust mixture.
This pattern of streams is maintained within every row of burners. The use of additional air pipe wall protects the waterwall tubes against high temperature corrosion at the level of burners. The advantage is NOx reduction rate exceeding 50%, high flame stability and long lifetime guaranteed by the use of heat-resistant and abrasion-resistant materials.
Boiler modernization with ECOENERGIA burners using a modified secondary air system allows to meet the requirements of new environmental standards for NOx emissions. The burners are protected by copyright and patented.
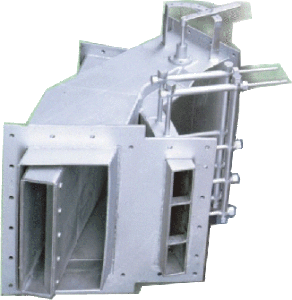
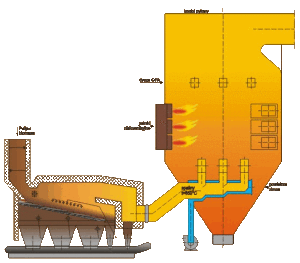
The combustion pre-chamber for biomass for coal dust boiler is a proprietary solution of ECOENERGIA filed with the Patent Office.
The pre-chamber allows you to use the enthalpy of the exhaust from the combustion of biomass for green energy products in the existing boiler.
The boiler works at the primary fuel, and biomass is only a supplement.
The pre-chamber allows the combustion of biomass with different moisture content, calories and granulation and various origin such as wood chips, wood dust, segregated waste, energy crops, etc.
The stability of pulverized coal combustion process is guaranteed by the optimal location of the exhaust nozzle from the pre-chamber in the slag hopper of the boiler. The pre-chamber interaction with dust boiler with low nitrogen oxide emissions burners can reduce NOx and protects the boiler screens against corrosion. Nominal heat output of 5 to 15 MWt.
ECOENERGIA Sp. z o.o. Warsaw offers:
Comprehensive modernization of power boilers in deep emission reductions of nitrogen oxides below 200 mg/Nm3 by using primary and selective non-catalytic reduction methods – SNCR.
Ecoenergia introduces turnkey projects reducing emissions of nitrogen oxides.
Our offer includes all stages, processes and investment industries:
- pre-modernization measurements,
- technical advice on the selection of an optimal method for NOx emission reduction for a particular boiler,
- designs for all sectors,
- comprehensive implementation (delivery and installation),
- start-up and optimization of the combustion process,
- warranty and after-warranty services.
The offered SNCR installations are based on our own proven technical solutions. Selective non-catalytic chemical process of NOx emission reduction uses the reductive properties of the reactants such as ammonia and urea.
PROCESSES
The efficiency of the process is dependent on the temperature occurring at the point of injection of urea. The ideal thermal conditions are between 850 °C and 1100 °C. If the temperature in the combustion chamber is too high, radical oxidation of ammonium formed from urea in the NOx ocurs, that can cause an increase in the concentration of NOx in the exhaust. If the temperature is too low ammonium radicals do not react with the NOx, which may lead to penetration of ammonia (NH3) into the atmosphere as so called “ammonium effect”. In addition, the NOx reduction will be incomplete if urea is not injected into the entire reaction zone.
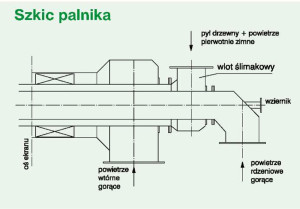
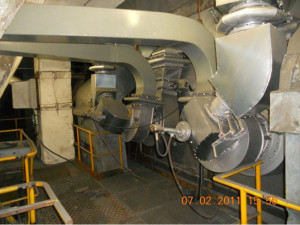
ECOENERGIA biomass burners for biomass dust enable burning biomass directly in the coal boilers or other furnaces.
- The burners are mounted in the belt of coal-fired burner or burners in the combustion zone of the boiler grate.
- Fine grinding dust is required (particles smaller than 3 mm) and low humidity (about 12%).
- Transport of dust to the burner is realised by a pneumatic system. Dust nozzle is equiped with the elements to stabilize the flame at the outlet.
- The combustion air is supplied from the nozzle and the outer core nozzle with turbulators.
- Nominal heat output from 2 to 12.5 MWt.
Ecoenergia offers a low-emission swirl burner for biomass co-firing (shredded waste wood, straw, rape meal, sunflower hulls and other agricultural products intended for energy) with coal or brown coal dust in a power boiler, having an extra dust nozzle embedded within low-emission swirl burner of coal dust, especially dust swirl burner with an internal separation of coal dust, preferably a NSW type.
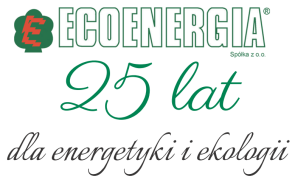